Industrial IoT, Edge Computing and Data Streams: A Comprehensive Guide
Aug 20, 2023
An introduction to IoT, Edge Computing and Streams for process improvers:
- What it means and why it matters
- Benefits and implementation best practices
- Converging Operational Technology with IoT to drive automation
Part One: What it means and why it matters
Collect, analyze and action data at the source
With the Industrial Internet of Things (IIoT) and edge computing markets projected to grow from USD 3.6 billion in 2020 to USD 15.7 billion by 2025, having an IoT strategy in place is becoming key to developing a successful IT roadmap in manufacturing, utilities, and a host of other industries. The ability to implement smart technology into industrial assets is revolutionary for data collection, analysis, and automation.
Now advances in edge computing mean equipment and devices can process data and action operations right at the edge of your systems. The 'Edge' is where your IT infrastructure meets the physical world, for example where a saw is monitored and controlled by computer to make precision cuts.
The benefit of moving computation to the Edge is you no longer need to wait for a reaction from a remote centralized database system, greatly reducing latency and allowing for near-instantaneous reaction times. This article will clear up what these emerging technologies mean for forward-thinking business analysts and operation managers as we plan for the future of IoT.
In addition Flowfinity Streams IoT data collection empowers you to record incremental high-frequency data at blistering speeds while storage and visualization are optimized for billions of data records. Meanwhile advances in the Flowfinity M1 Controller such as Fast Track IO mean you can measure sensor activity with sub-millisecond accuracy to ensure near real-time monitoring and react to sensor inputs near-instantaneous response time.
What is the Industrial Internet of Things (IIoT)?
One of the biggest trends in both consumer and industrial tech is the continued emergence and adoption of the Internet of Things (IoT).
It's useful to think about IoT as networks of physical objects that can sense their internal states or external environment and then autonomously communicate or respond to change as needed.
For example, smart home devices are an increasingly common consumer application of IoT. Internet-enabled home automation devices can help you save money and reduce waste by allowing you to control appliances, lights, and heating from your smartphone, or by sending alerts and making adjustments based on set parameters.
The Industrial Internet of Things (IIoT) focuses on applying these principles in industrial settings, connecting everything from machines in a factory to sensors in a laboratory and any other mechanical or electronic equipment that needs monitoring.
If you can connect these internet-enabled devices and sensors to a business process management system you're now able to collect and process more data than ever, analyze all that data in real-time, and ultimately make better data-driven operational decisions. Industrial IoT solutions also empower organizations to transform business processes by automating monitoring and emergency response procedures, which has the potential to unlock tremendous value through efficiency and precision control.
Edge Computing revolution
Gartner defines edge computing as 'part of a distributed computing topology where information processing is located close to the edge, where things and people produce or consume that information.'
But to understand why organizations would want to use edge computing, it may be more useful to focus on the word 'processing.' Edge computing allows organizations to capture, analyze, and action data at or near the source. In other words, the edge is where your digital systems interact with the physical world.
The reason why edge computing has become such a hot topic is because of the explosive growth of IoT. Sometimes edge computing and IoT are presented as if they are synonymous, however that's not the case.
Organizations are deploying more and more IoT devices such as internet-enabled CCTV cameras and sensors monitoring physical assets. These devices can send the data they capture and, in some cases, receive data, generally from a central server.
Edge computing takes this a step further by including processing power at the site of these devices so that the data management, analysis, and decision-making capability happens instantaneously right where IoT devices collect this data at the 'edge' of your network, instead of in an offsite server.
Edge computing utilizes IoT devices for data collection, but not all IoT devices are capable of edge computing. An organization can collect more data and make better, faster use of IoT data when they deploy edge computing. The question for organizations is how can they best make use of the unprecedented volumes of data and new workflow opportunities that IoT generates?
Edge computing helps you overcome challenges associated with latency and inefficiency when transferring data between your connected devices and your data center or cloud infrastructure. As more organizations look to connect their physical assets to their digital systems, forward-thinking organizations can benefit from the speed and accuracy gained by pushing their decision-making out to the edge.
That said Flowfinity Streams allows you to collect, store and analyze vast amounts of machine generated data with remarkable speed and efficiency, giving you the best of both worlds, sub-second response time with long-term storage and time-series visualization capability.
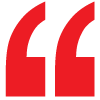
Gartner predicts that by 2025, three-quarters of enterprise-generated data will be created and processed at the edge – outside a traditional centralized data center or cloud.
Deploying IoT with an Edge
The extent of an IoT deployment and where the 'edge' is will depend on your organization and industry as the potential use cases are limited only by your imagination. For most organizations, the architecture will require data collection sensors, internet-enabled controllers and a reliable network connection. After that, how these devices are deployed will change depending on what your organization wants to achieve.
A manufacturing use case with proven ROI is to deploy sensors to monitor machinery and equipment status in real-time. When coupled with controllers that feature processing capability and are connected to your process management system you transcend basic data collection and can deploy an efficient and reliable edge computing solution to replace time-consuming and error-prone human maintenance inspection routines with automated preventative maintenance and situational awareness.
Utilities also have multiple use cases where edge enabled IoT can lead to significant operational efficiencies. Water and wastewater service providers need to monitor pumping station equipment, respond to water flow volumes, and keep water samples stored within acceptable temperature ranges.
Deploying data collection sensors connected to controllers and SCADA systems provides full-time monitoring for preventative maintenance and automated alerts that save time and effort, especially when faced with an emergency or system failure.
There are many other possibilities for any industry as IoT enables edge computing solutions to proliferate. The reality is that to future-proof your systems, most organizations will benefit from deploying connected IoT devices made more powerful when they can process data and initiate corrective action at the edge, while having efficient storage and access to millions of records through Flowfinity Streams.
Part Two: Benefits and implementation best practices
Adopting the Industrial Internet of Things
As the pace of technological change intensifies forward-thinking organizations are constantly looking for ways to improve their data collection and processing capabilities to increase both the quantity and quality of data to make better, more timely decisions.
In a recent survey conducted by Microsoft, roughly 85% of respondents say they're currently in the midst of IoT adoption, and three-fourths have projects in the planning stages. An equally high percentage — 88% — believe that IoT is 'critical' to their business' success, with a majority of those who've adopted IoT predicting they will see a 30% return on investment.
To do this you can leverage industrial IoT solutions from Flowfinity to improve monitoring capability by adding sensors to machinery and other assets that capture performance data and feed it back to a process management application in real-time, without the need to manually program the physical devices or write code to enable data streaming and workflow automation.
With this real-time asset data in place, you can leverage these streams of information to make more timely and informed decisions. A manufacturer may use machinery performance data to transition to more proactive forms of asset management where preventative or predictive maintenance becomes the norm, greatly reducing downtime and prolonging the life of their equipment to drive significant return on investment gains.
This access to more, better quality data can help in other ways too. Business analysts are provided with improved insights to meaningfully reshape business processes. Managers and team leaders can more readily improve operational performance and make faster decisions. Workers can increase their productivity and reduce downtime while doing away with laborious manual inspection procedures.
The benefits are many, however, to fully reap the rewards your IoT systems must be properly configured and integrated into your digital workflows. Meanwhile, controllers must have the capacity to process information and trigger automated responses from the edge of your system at the point of data collection for maximum efficiency.
Industrial IoT deployment challenges
A successful IoT and data management system must be flexible enough to meet your unique requirements, yet not so complex to source and implement that the effort outweighs the benefit, or the project simply stalls out and fails. A major challenge with IoT deployments is that to get the components integrated with your equipment and systems custom code is often required.
Implementation complexity is one of the reasons that Microsoft reports 30% of IoT projects fail in the proof-of-concept stage, often because the implementation became too expensive or the bottom-line benefits were unclear.
This is a significant barrier to entry as the costs of programming can be prohibitive and long development cycles risk delays and disruption to the final deployment. Many firms also lack the expertise to maintain and modify these systems as time goes on and risk losing their investment or failing to maximize the potential.
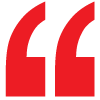
Microsoft reports that complexity and technical challenges are an IoT dealbreaker for 38% of decision-makers they surveyed, and that 47% believe there aren’t enough available skilled workers to build or maintain a network of connected devices.
On the other hand, off-the-shelf solutions can be deployed quickly but can lack the flexibility to tie sensor data together with existing business process management systems and don't provide true edge capability, or lack the streaming functionality needed to collect, analyze and store the vast data volumes that can be generated.
3 best practices to ensure IoT deployment success:
1. It should be easy to deploy an IoT network of sensors for remote monitoring without writing code to avoid needless technical complications that can make the project prohibitively expensive or time-consuming.
2. Data from sensors should be directly streamed to workflow applications that manage business processes and feed interactive reporting dashboards. Sensor data that exists in a silo unconnected to the rest of the organization is of little value and properly integrating with existing business process applications can be a significant challenge if hardware and systems were not designed with native compatibility.
3. Any controllers deployed to collect and action sensor data should also be edge computing capable devices that can be configured to pre-process data. This conserves bandwidth, reduces latency and ensures machine operations are triggered in real-time. For sensor data that needs to be sent to a server ensure you have data stream capability with ample bandwidth and storage.
Flowfinity IoT solutions can be quickly configured, integrated, and deployed seamlessly into a business process management solution. This end-to-end solution draws data from the edge into your workflow applications and reporting dashboards. Therefore, corrective actions and notifications are efficiently automated, giving managers instant access to sensor data so they can make timely, effective decisions that will improve performance and boost the bottom line.
No-Code IoT, Edge Computing and Streams
IoT devices and edge computing controllers can now be combined with no-code application configuration tools, such as Flowfinity, offering a unique opportunity to create truly end-to-end workflow solutions without the cost and complexity of custom code. Now you are empowered to configure devices and systems that take data from the edge and seamlessly integrate it into one unified workflow and data management platform right out of the box.
Given the potential impact these new technologies will have on business processes, forward-thinking organizations will look to process experts such as operations managers and business analysts to drive edge computing strategies. By adopting intuitive no-code app and device configuration, these citizen developers can be the ones to define business processes that run on the edge – something that previously would require specialist IoT programming skills.
A no-code approach will also help your organization remain flexible and iterative. As process efficiencies emerge thanks to this new data, no-code edge computing solutions will allow for quicker testing and deployment. Whereas custom coded edge computing ecosystems will suffer from costly and delayed development cycles.
Edge devices can produce constant streams of data that would be difficult or impossible to put into a useful context without visualization. With no-code app development, business analysts and operations managers can create and iterate interactive dashboards that monitor operations visually and in real-time. This flexibility will be vital in making the most of edge computing.
Flowfinity Streams was designed to work natively with Flowfinity controllers and optimized to store time series data from sensors and other automated data sources using substantially less space compared to traditional relational data storage models.
As IoT and edge computing align to create new areas of opportunity, business analysts, operations managers and IT leaders can deliver value by improving how organizations execute their processes while helping shape the technology road map to ensure long-term benefits and ROI.
Part Three: Converging traditional Operational Technology with IoT to drive automation
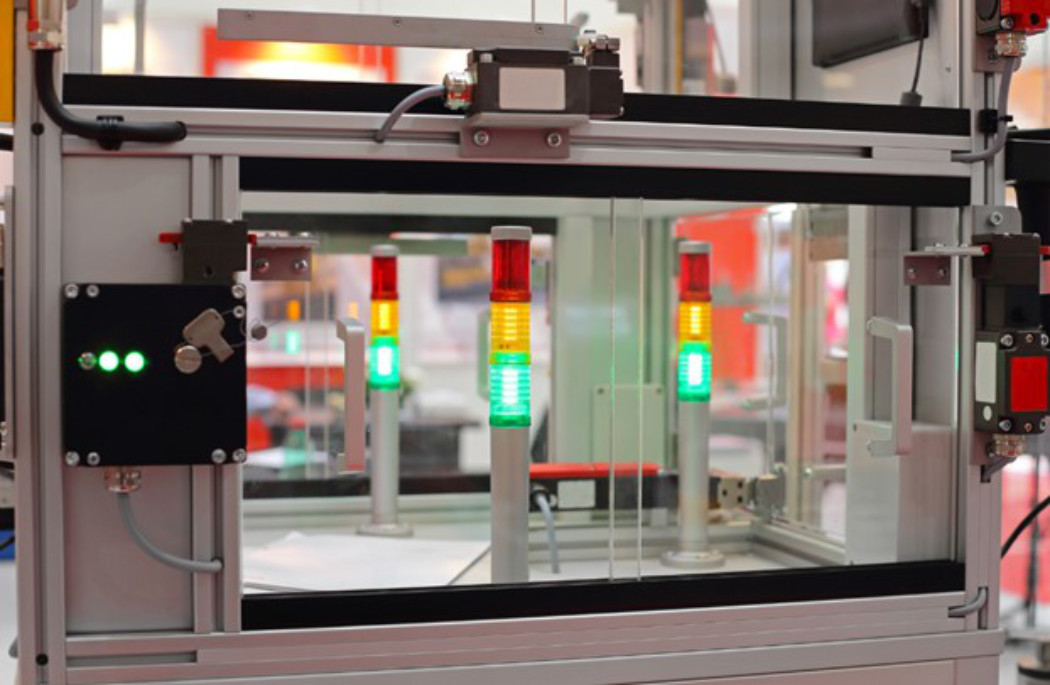
IT / OT Convergence through IoT
The fusion of Operational Technology and Information Technology is often touted as the upcoming Fourth Industrial Revolution and is predicted to be the key driver of digital transformation in coming years for the manufacturing, logistics, utilities, building management, and other industrial sectors.
Operational technology (OT) is the term coined to describe the Industrial Control Systems that have been adopted in many industries to monitor and control industrial assets. For example, the oil & gas industry and water utilities have used Supervisory Control and Data Acquisition (SCADA) systems for years.
However, in many organizations these OT systems are aging, maintenance is time consuming, and they could be made more efficient if properly integrated with digital process management workflows. The challenge is that the specialization required to modernize in the short term prevents organizations from effectively future-proofing their operations for the long.
What modern IoT solutions offer is the chance to reimagine and modernize your OT systems, ensuring the same reliability, but with increased insight into real-time operations. Additionally, you'll reduce the ongoing costs and labor associated with maintaining the complex and rigid integrations required to run and update existing centralized or distributed relay-based control systems.
The ability to procure pre-configured controllers with internal processing power and built-in database and workflow integrations is a new and exciting complement to existing OT infrastructure that allows new capabilities to be added with much less effort and difficulty than ever before. For example, you can now easily configure dashboards to visualize real-time sensor data. When coupled with exiting SCADA systems you can analyze large quantities of data quickly and at scale, a major improvement if you are running a large physically distributed utility or manufacturing facility.
By embracing IIoT and edge computing, business analysts, operations managers, and IT professionals can now combine both the IT and OT aspects of their systems in one unified platform configured without code. This allows organizations to benefit from timely data-driven decisions and automated workflows without having to design and program the data collection and workflow aspects of a custom system.
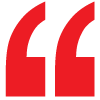
Analysts, journalists and others agree that the convergence of Information Technology (IT) with Operational Technology (OT) is one of the key drivers of digital transformation. Yet many people are confused about the IIoT, and how to implement a successful adoption strategy. (source)
Driving automation with IoT at the Edge and Streams
Edge computing, moving data processing from data centers out to the edge, where your real-world data is being collected, offers even further benefits.
For example, reduced latency is a significant benefit of edge computing, allowing faster decision-making as organizations reduce the time spent transmitting and processing data. Edge devices, such as controllers with built-in processing power, allow organizations to aggregate and action data at the source instead of at a remote central database. Therefore, your workflows aren't delayed by latency issues when a large volume of data is transferred from the collection point back to your processing center. This will streamline your business processes, allow automated responsive action to happen faster, and greatly reduce the likelihood of a catastrophic event.
Smart controllers also drive efficiency and preventative maintenance by speeding up the human elements of a business process. For example, in a wastewater facility, a controller connected to a tower light can create a clear signal to laboratory technicians that immediate action is required the second a sample falls out of temperature range or a piece of crucial equipment fails.
The ability to trigger instant notifications and interact with physical assets helps organizations create more predictive and preventative maintenance workflows. For example, at a manufacturing facility, an organization may have previously assigned employees to routinely monitor the performance and calibration of machinery to ensure it meets safety and performance expectations. If during a routine inspection, a piece of equipment is found to be out of calibration, an employee can act to shut down production and then request maintenance.
This standard process is now obsolete because it cannot prevent machinery from running in an unsafe or damaging way for a prolonged period before the fault is discovered manually.
By implanting an IoT solution a sensor can collect operation data many times a minute. As soon a machine falls out of an acceptable range, an edge device automatically flags the error and creates a maintenance order in a workflow solution. This allows an employee to step in to perform an assessment quickly and take corrective action to prevent a serious malfunction, or accurately predict when a future maintenance cycle should be scheduled to optimize up time.
Prevention happens even faster when actions are automated, and the processing is performed at the edge where the machine is operating. When rapid cycle manufacturing equipment falls out of alignment milliseconds can make the difference between a quick repair and a costly replacement. In many environments, even marginal changes in temperature or vibrations can indicate potentially damaging issues, so latency concerns take on an even greater significance.
In these cases, an edge controller device can act where a simple IoT sensor cannot, shutting the asset off or activating a tower light to indicate potential issues. This is extremely useful for mitigating risk and preventing costly or dangerous errors.
The Flowfinity M1 Controller offers this important functionality, taking control of a physical asset while also instantly launching the appropriate workflow actions and recording data. This combination of Industrial IoT and edge computing functionality allows organizations to create an unprecedented level of automation to support a truly preventative maintenance process, while Flowfinity Streams empowers you to store and analyze this data over the long term to optimize operational intelligence.

IoT Edge Computing savings and security
Edge-enabled IoT can also provide a cost-effective solution to automating business processes long-term. Edge devices gather and action data constantly, going well beyond the ability of humans to make manual observations. These devices allow you to use high-volume, high-frequency data collection coupled with data visualization tools such as interactive dashboards to find new efficiencies in your workflows and make better business decisions faster.
There are also significant savings to be realized via reduced bandwidth costs. When organizations begin aggregating data at the source, it allows for more efficient use of IoT devices without paying the significant data transmission costs to wireless network carriers since there is no need to upload to a central database for processing.
Edge devices, like the Flowfinity M1 controller, can be deployed to essentially transcribe data between physical objects and digital workflows, storing data on the device and never losing data due to connectivity issues. This kind of edge deployment provides extra resiliency to your IT infrastructure.
Consider a laboratory setting, deploying sensors is an efficient way to monitor environmental factors such as temperature or humidity. Currently, a lab could deploy IoT sensors to take frequent readings and upload these to a central database. But if power or internet-connectivity fails, there is likely to be a hole in your data right at the critical time, and your alerts could fail, leading to a delayed or disrupted response.
However, a controller with a separate power source or battery could still trigger a notification, launch a workflow action, and continue to store readings on the device, providing redundancy against a loss of power or connectivity. This is another example of how Industrial IoT and edge computing can improve overall resiliency and safeguard your mission-critical materials.
IoT devices and edge computing controllers can now be combined with no-code configuration tools, and efficient data streaming and storage solutions, offering a unique opportunity to create truly end-to-end workflows. Taking data from the edge and tying it together into one unified, configurable workflow and data management platform.
To discuss your IoT and edge computing strategy, contact our experts for a complimentary consultation.